- Aerospace
- Power Production
- Medical Industries
- Processing Food
- Automotive
- Construction
- Glass Production
- Stone Accessories
- Rubber and Foam
- Textiles and Clothing
Due to its unrivaled advantages in manufacturing, waterjet cutting is one of the most widely used cutting technologies. Cutting with CNC waterjet technology is utilized in various industry sectors, including aerospace, automotive, and marine. They can cut through multiple materials, including metal, glass, rubber, plastic, tile, and stone. Waterjet cutting’s adaptability makes it ideal for high-volume production, prototyping, and complex or tough cutting applications.
WHAT IS WATERJET CUTTING?
Waterjet cutting utilizes a high-pressure stream of water to cut materials by eroding a narrow line in a workpiece. A mixing chamber is filled with highly pressurized water shot through a diamond or ruby nozzle. This pressure produces a vacuum that pulls garnet sand into the stream, which is discharged along with the water at the target to be cut.
Abrasive components like aluminum oxide or sand garnet are used in this waterjet to increase cutting performance by generating cuts through abrasion rather than vaporization.
A waterjet cutter is a device with three basic parts that uses a high-pressure water stream to etch a precise line through a piece of material. Then, a granular type of abrasive is added to boost the cutting power of the waterjet. The type of abrasive media depends on the density and composition of the material, such as titanium. To make switching between cutting with only water and cutting with an abrasive material straightforward, the abrasive is applied at the nozzle. Three fundamental parts make up the waterjet cutting machine system:
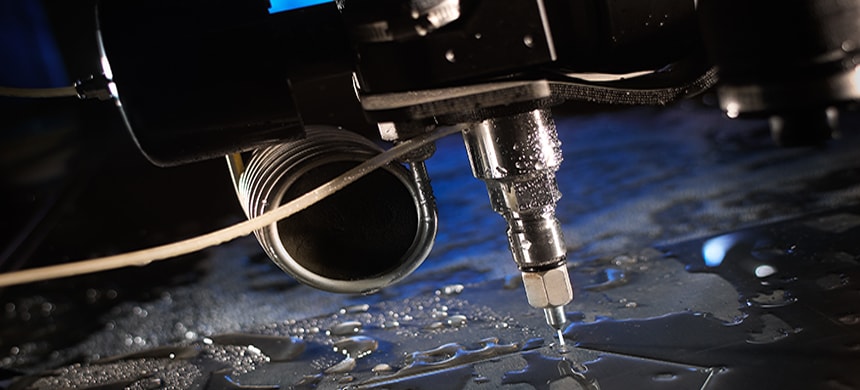
- Table: An X-Y nozzle mechanism with a garnet hopper attached and a catch tank below makes up the table.
- Pump: The high-pressure pump provides pressurized water to cut.
- Controller: The controller features software capable of operating the system, controlling motion, and positioning the nozzle during the waterjet cutting operation.
HOW DOES WATERJET CUTTING WORK?
The abrasive waterjet cutting nozzle’s mixing chamber and tube design enable the abrasive to properly mix in with the high-pressure water to enable effective cutting. Waterjet nozzles are also made without the abrasive mixing chamber and tube, so they can fire high-pressure water instead of the abrasive solution, which can cut considerably softer materials. Other materials that can be easily cut with precision using waterjet cutters include:
METALS








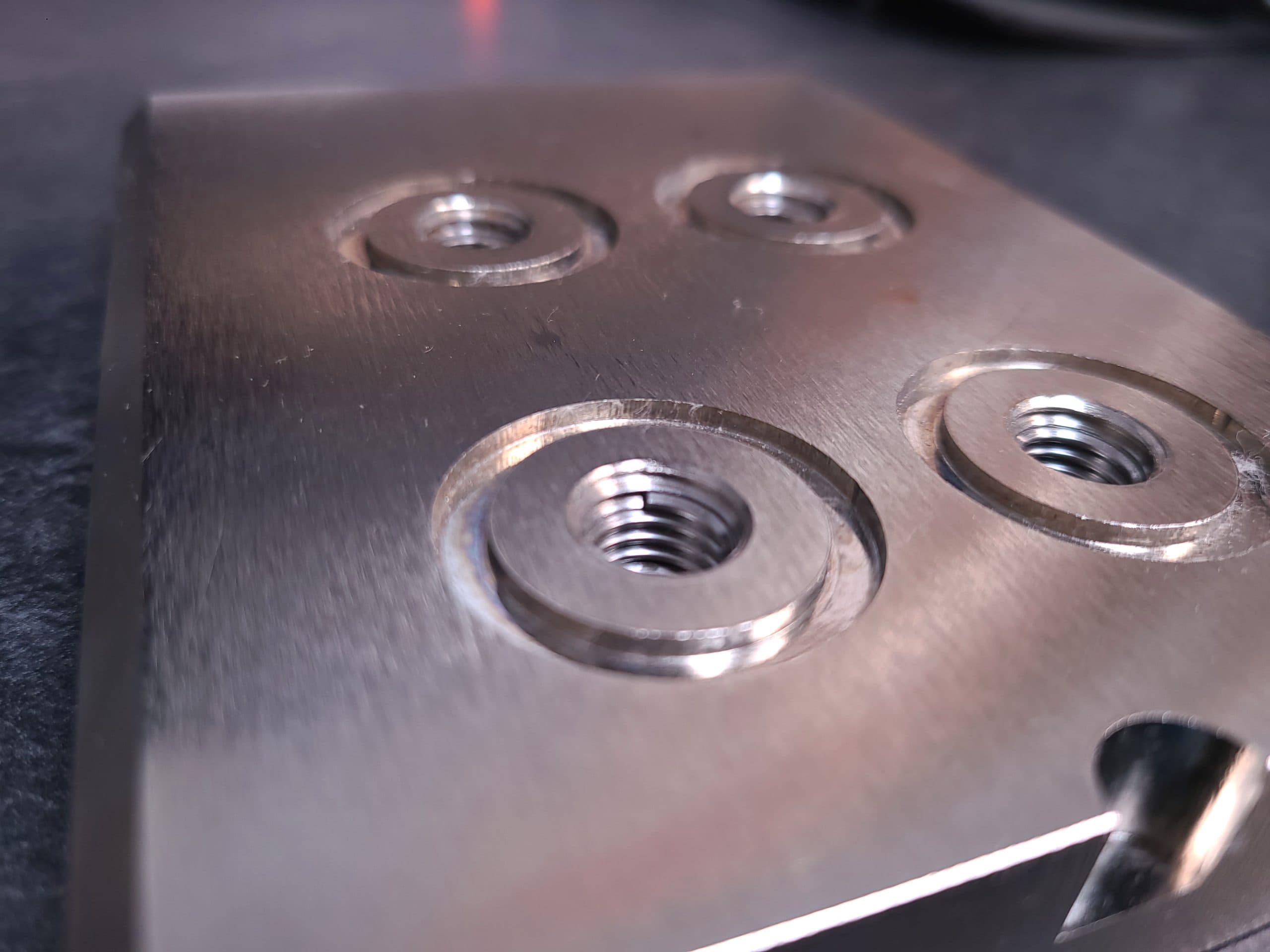
NON-METAL MATERIALS











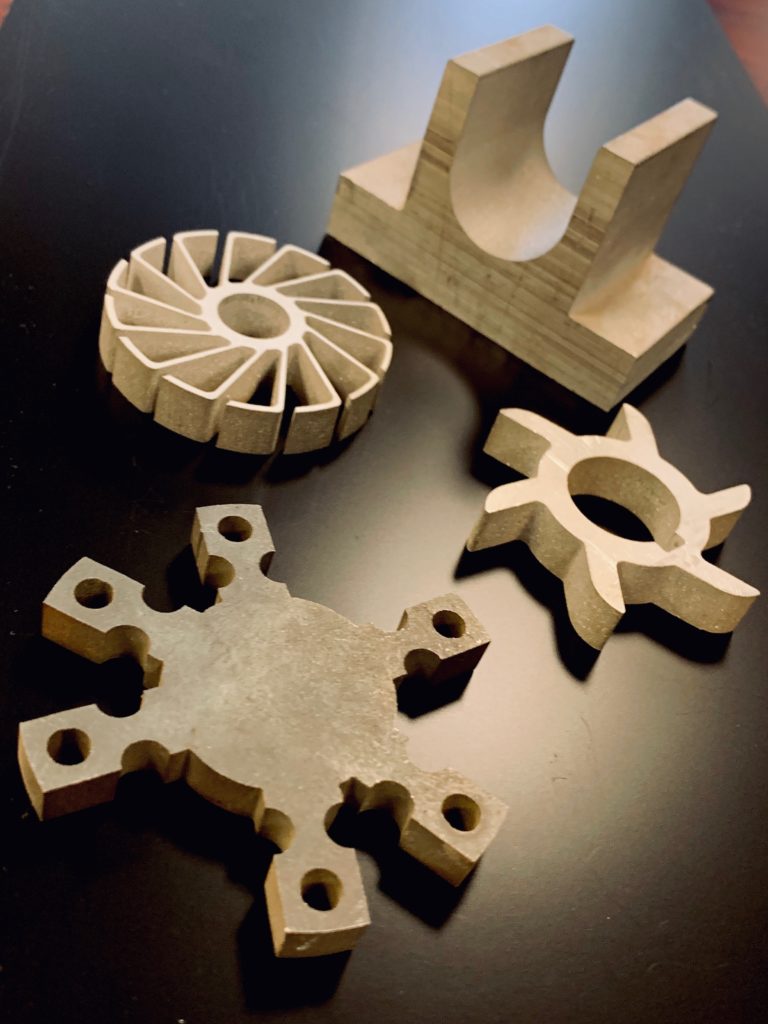
WATERJET CUTTING STEEL
Most materials, including stainless steel and carbon steel, may be carved through an abrasive waterjet machine 12 inches (30 cm) under normal circumstances. More can be cut utilizing sophisticated garnet-particle abrasive waterjets. Waterjet systems can be reconfigured to cut through 18-inch steel blocks.
When necessary, thick foam, rubber, and paper can all be sliced with pure waterjet technology. For a pure waterjet cutting foam, even foam and paper several feet thick are not a problem.
Pure waterjet cutting presents a challenge when attempting to cut tougher materials. Therefore, modern waterjets using abrasive waterjet cutting technology are preferable for thicker materials.
BENEFITS OF WATERJET CUTTING
Due to its high-pressure capabilities, waterjet cutting is generally more appropriate for thicker, tougher materials than laser cutting. Below are a few advantages of using a waterjet cutting technique:
- HIGH LEVEL OF EDGE QUALITYThe edge quality offered by waterjet cutting is one of the main benefits. An extremely thin beam of water impacts the workpiece during waterjet cutting. As a result, our object is not being ground against metal cutters. As a result, the finishing is clean, and the edge quality is outstanding.
- EFFICIENTMany people may be unaware that waterjet cutting allows you to simultaneously cut many layers of material by stacking them on top of one another. Waterjet cutting is more effective than any other cutting method due to this stacking ability.
For instance, you might use a waterjet cutter to cut six layers in the time it would take to cut one layer of a stone slab. As a result, the price and time would be reduced by approximately a third, making the procedure very effective and affordable. - BETTER ACCURACYCutting tolerance is the deviation from the planned cut in the cutting process’ location. Cutting tolerance, said simply, determines how exact (or inaccurate) the cutting process is. The cutting precision increases as the tolerance decreases.
- CONSISTENT TOOLINGYou can insert a fresh workpiece or even a different material without changing your tools when using waterjet cutting. You don’t need to adjust settings for a fresh workpiece made of the same material. You can modify the settings in the software itself for new materials.
TYPES OF WATERJET CUTTING SERVICES
Waterjet cutting has gained immense popularity in domestic and commercial settings. It can be applied to various tasks and requirements in the manufacturing, construction, and building industries. Here are the types of waterjet cutting services available in the market:
WATER ONLY CUTTING
The process of pure waterjet cutting requires only pure water using the pressurization of the pump to achieve the desired cutting.. Soft and medium-hard materials respond best to this procedure. Soft and hard to machine materials like foam, rubber, and plastics are ideal for water only cutting.
ABRASIVE WATERJET CUTTING
An abrasive waterjet cutting machine adds abrasive to the water for a more dynamic cut. You need to add three more components to turn a pure waterjet into an abrasive one.
- Abrasive focused nozzle
- Cutting-edge mixing platform
- Pure water focusing nozzle
You will also require an abrasive substance. The pure water nozzle’s main job is to create a jet of highly compressed water. The jet then travels at a speed of 1000 m/s through the water to the abrasive mixing chamber.
INDUSTRY APPLICATIONS
Any metal, including aluminum, hardened tool steel, titanium, copper, brass, and other rare metals, can be cut using waterjet technology. Because waterjet cutting does not raise the temperature of the workpiece, the workpiece’s structural and chemical integrity is not compromised. Waterjet cutting is also a preferred manufacturing technique in the following industries:

WATERJET CUTTING SERVICES BY MET MANUFACTURING GROUP
MET appreciates collaborating with customer engineering departments to validate and enhance the design of the items we produce and supply. OMAX Waterjet devices use Intelli-MAX, which is OMAX-exclusive software that imports virtually any type of cad file.
Together with our extensive knowledge and experience in handling high-end waterjet cutting machines, we are one of Indiana’s leading names for precision manufacturing.
Our team is excited to work with you. Contact us today and see how our experts can help you.